Ampac USA Shares Insightful Piece on Wastewater Treatment in Cheese Production
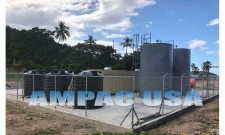
MONTCLAIR, Calif., November 17, 2018 (Newswire.com) - AMPAC USA Sharing here some thoughts now it has turned out to be a PR nightmare for many companies. With regional and state restrictions on the water quality that is discharged, companies are now required to treat their water before rejecting it. A great step towards helping save the environment, this has posed a challenge for the management of big cheese producers from a business point of view. In certain instances, companies seem to have limits on meeting the stringent regulations of wastewater treatment. An example of Carbery, however, shows light on how it can benefit the companies and its image. Taking it positively, Ampac USA and others are now investing in advancements that help them achieve their goals with an eco-friendly approach.
Description:
The kind of restrictions placed on industries these days are stringent than they were before. It has forced companies to look at options that are not only resource-intensive but are good at returns too. And a wastewater treatment facility provides them with just that.
Sammy Farag, CEO, AMPAC USA
Ampac USA is a water treatment systems manufacturer that has worked in the field for decades now. Over the course of time, they have come across several challenges that have helped them improve the way they build water treatment products. Food and Dairy industry has been one such challenge over their years of experience. Cheese production at that is one of the controversial subjects when it comes to water.
The cheesy connection
In a recent story of Analysis of fatty residue in pottery on the Dalmatian coast in Croatia placed the use of cheese and fermented products around 7200 years ago. 500 years before that, evidence suggests that only milk was used for hydration of children. Today cheese has become an essential part of an average American’s diet. It’s a grilled cheese sandwich for breakfast, cottage cheese in the Caesar salad you order for lunch and melted parmesan or mozzarella in lasagna you have for dinner. Food without cheese is even unimaginable for many.
Although the growth in cheese consumption has been fairly normal in the past 17 years, in the U.S. alone the per capita cheese consumption is 39 pounds. A figure even more intimidating is one million pounds of cheese sitting in freezers worth $150 million because the global market for the same is saturated. Pizza, a favorite snack for practically every American is a major contributor to the industry. 70,000 pizzerias in the U.S. contribute to the already growing $45 billion dairy industry. On top of that, The Agriculture department in 2016 bought $20 million worth of cheese for food banks.
Cheese and production
Production of cheese doesn’t directly involve water and a large portion involved is milk. However, if milk is produced specifically for cheese, for every gallon of milk, 1.5 gallons of water is used which makes cheese water consuming indirectly. The production is done through fermentation and coagulation of milk where it is concentrated. The major ingredients are casein and fat. The average ratio between milk and actual cheese is 10:1. The whole process is intensive and follows coagulation using microorganisms and acidifying bacteria, releasing the whey and ripening the cheese.
After this production, the wastewater produced contains BOD and COD in high amounts. The whey water which remains after removal of whey solids is high on nitrogen content. Add to that the phosphorous which enters the wastewater through the phosphorous-based cleaners used for cleaning processes. This combination of nitrogen and phosphorous is highly dangerous for the environment. The phosphorous is harmful to the processes too as it clocks pipes and decreases efficiency.
Regional authorities and state regulations have forced companies to look at options to treat this water. Recently, new laws made to protect the Northwestern river basin threatened the business of a major cheese producing company when they kept exceptionally low levels of effluents in wastewater. Some of these are BOD limits below 3 mg/L, total nitrogen limits below 1 mg/L and total phosphorus limits below 0.07 mg/L.
Whey-stewater Treatment to the rescue
Treatment of the Whey in wastewater from industries is a growing trend now. Companies are investing capital resources in treatment systems that help them achieve the required levels of effluents in their wastewater. Cheese producing companies have been building large wastewater treatment facilities to treat the water and use the recycled water for many other purposes.
Sammy Farag, the CEO of Ampac USA that builds Industrial level wastewater systems and is a consultant for large-scale wastewater treatment facilities could not agree more. “The kind of restrictions placed on industries these days are stringent than they were before. This is owed to the increased environmental harm caused by something as simple as cheese production even. It has forced companies to look at options that are not only resource-intensive but are good at returns too. And a wastewater treatment facility provides them with just that.”
Considering a company installs one such facility, the benefits are tremendous. Using the globally accepted safe and quality performance of the Reverse Osmosis process, the system is able to reduce the number of effluents fairly down to the required levels. A little chemical treatment after this can ensure the elimination of hazardous elements in the rejected wastewater completely. This is not only helpful in sticking to the regulations, but if dug deeper, a lot of the rejected waste can be reused thereby decreasing wastage.
Carbery Milk Products is an international food and cheese manufacturer situated in Ireland. The company has operations in the U.S. too and uses a treatment plant with various advantages other than meeting the water quality standards of wastewater. This can be done in the following ways:
1. Ethanol production: Converting whey to ethanol and then using it as a feedstock for economic biofuel production. Carbery now sells 660,000 gallons of bioethanol to an oil company for E5 and E85 blends.
2. Phosphorous from this plant is recovered as a sludge product from the dissolved air flotation process and is used as a fertilizer in agriculture as a non-renewable resource.
3. Wastewater in Carbery is also treated for water that can be reused and inducted in either the RO plant again or the production process. The reused water when treated with oxidation and sent into RO plant can be a membrane cleaner and increase the membrane life.
Carbery plant reused even the BOD. In dairy wastewater, 1 kg BOD is equivalent to 9.3 L of full-fat milk. By converting BOD loading back to a milk-equivalent and then applying a nominal price of say 30 cents per liter of milk, it is possible to show the cost of the product - and that does not include the wasted thermal energy and other costs that went into processing it. The company achieved a 30 percent reduction in lost product and annual savings of $1.7 million as stated by the O2 Environmental’s research.
Ampac USA’s wastewater treatment product like the Industrial wastewater treatment plant is made especially for intense challenges like these. The AP-WTS-5 is a Dynamic sequencing batch reactor system designed for biological and chemical treatment of wastewater discharge. The package comes with all process equipment components; including pretreatment, disinfection, effluent recycling Systems. It benefits the industry with its ease of manual operation, lower operation costs, and less space requirement. Apart from that, it is capable of handling wide swings in hydraulic and organic loading. A perfect answer to wastewater treatment, it can assist a factory to be self-sustainable and nature-friendly.
It is possible to be environmentally responsible and to be able to save huge on the rejected water as proved by the company. Treating the wastewater can have a positive impact on the company’s books as well as goodwill among customers. Our favorite snack and that too eco-friendly, what better way to enjoy the richness of cheddar or parmesan without the environmental consequences.
Source: AMPAC USA