With Westfall's High-Performing Static Mixers, Big Industry Engineers Break Rules, Improve Results and Cut Water Costs
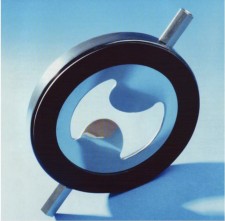
Bristol, RI, April 6, 2017 (Newswire.com) - The need for lower cost water is inspiring today's Big Industry engineers to push Westfall's Static Mixers beyond traditional engineering limits.
Originally developed for use in municipal wastewater treatment systems. Westfall’s Static Mixers excel at mixing disinfectants evenly across the flow stream, and at thoroughly blending flocculation polymers used to remove suspended solids. The motionless mixers are durable enough to last up to 40 years with little to no maintenance.
We don't usually push our mixers to out-perform textbook uses. We're grateful to today's pioneering engineers who are willing to break the rules and get these extraordinary results.
Bob Glanville, President
Engineers in other industries have been attracted by Westfall’s range of applications and are pushing the mixers’ performance levels to solve costly water problems.
One customer is leading the way at hydraulic fracturing sites where clean water is at a premium. With the customer’s portable water treatment unit, used fracking water is recycled through Westfall’s Static Plate Mixer 2800. The rule-breaker is that undiluted, high-density polymer is injected directly into the fracking water without the standard pretreatment. This engineer took a chance that Westfall’s plate mixer would be effective enough to distribute the high-viscosity polymer evenly across the flow stream, so suspended solids could be flocculated for removal. This gamble is paying off. Westfall’s customer saves money by injecting the polymer neat and skipping the use of coagulants. The drilling company saves money by having low-cost produced water on site to recycle through its fracking operations.
Another customer makes liquid mud for use as a lubricant in drilling offshore oil and gas wells. Their high-density, undiluted mud is barged to the well site. At the site, two of Westfall’s Plate Mixers Model 2800 are installed sequentially in a 6-inch pipe. The untreated mud is pumped through the two mixers, along with enough ambient seawater to produce the desired viscosity. This customer took a chance that Westfall’s compact plate mixers could emulsify untreated high-density mud with salt water. The application saved the customer the standard cost of transporting diluted drill mud and water to the site, as well as premixing and storage costs.
A third customer treats wastewater at a large poultry processing plant. This company took a chance and replaced their standard serpentine piping with Westfall’s Low Headloss Mixer 3050 inserted into a short, straight, pipe. In this case, less polymer was required for flocculation. Less space was required because extensive serpentine piping was replaced. Less energy was required because of the Static Mixer’s reduced headloss compared to the serpentine pipe. Breaking the rules allowed this company to save money, space and energy on its wastewater treatment system.
With these money-saving solutions, developed by Big Industry engineers using Westfall Static Mixers, the high cost of water for processing use (as well as regulatory compliance) is becoming less and less of a problem.
WestfallStaticMixers.com
Source: Westfall Manufacturing Inc.