Building Green in 2017
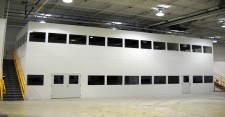
Blairsville, GA, June 20, 2017 (Newswire.com) - Traditional construction faces many issues when it comes to the handling, creation, and recycling of wasted materials. In fact, an NAHB study found that an estimated 8,000 lbs of waste are created from the construction of a 2,000-square foot building. These squandered materials are all standard materials that are used to construct a building: wood, brick, insulation, drywall, etc. However, only an estimated 20% of these leftover construction materials are actually re-purposed or recycled, according to The American Institute of Architects. On top of that, the AIA states that “it is estimated that anywhere from 25 to 40 percent of the national solid waste stream is building-related waste.”[1] And in 2009 the Construction Materials Recycling Association, estimated that construction and demolition waste from building construction was around 325 million tons annually. So, in a society that constantly pushes for greener solutions across all facets of life, what alternatives do companies have to be more eco-friendly?
Modular Sustainability
The processes that go into modular construction allow for far more accountable and ecological building methods. Modular construction takes advantage of a process known as “Mass Customization.” When constructing a modular building, the same paneling that used to create one building can be snapped into place on another building. However, the building can still be designed however needed! Therefore, any paneling left unused after a job can simply be used on the next one. Plus, the panels will not need to be moved very far because all structures are built in their own facilities, ensuring they will not go to waste. And we use CAD software to map out all the prefabricated projects, so we know the exact amount of materials that need to go into each job.
The factory setting also allows the company to better control the inventory and regulate the working conditions, in comparison to traditional construction. While most construction sites have delays due to inclement weather, the modular construction process takes place indoors, keeping the moisture levels low in the materials, preventing damage. While the employees construct the building indoors, the project site is being set up for installation. Therefore, with these two processes occurring simultaneously, the building site receives far less disturbance from foot traffic, machinery, equipment, and materials.
Ultimately, the same paneling that allows modular construction companies to use Mass Customization also supports recycling efforts. The buildings are designed to be installed and disassembled easily. So, when a building is no longer of use, instead of being demolished like traditional construction, the paneling can simply be taken apart and reused. This allows the company to drastically cut down on waste in the deconstruction process as well. Many of the structures are also movable, so the same building can be moved to another location to serve another purpose.
Source
1) http://www.aia.org/aiaucmp/groups/secure/documents/pdf/aiap072739.pdf
Source: Panel Built Inc